Whether you’re a professional or a keen DIYer, chances are you’ll need a selection of screws for that next big job. But with so many types of screw available, each one designed for a different material and surface, making the right choice for your project can be a nightmare!
When you’re considering which type of screw you need, there are a few main things to consider. Firstly, you need to choose the right type of screw. Choosing the wrong screw type for the job can damage your surfaces, your tools, and the screw itself.
Secondly, make sure to choose the right size screw. A screw that’s too short won’t hold the materials together, while a screw that’s too long could go right the way through the material or damage wiring or pipework in walls or floors. Similarly, a thick screw may damage brittle surfaces, while a thin screw might not be strong enough for the job.
Finally, consider the screw features. This includes the drive type, the head type, the material, thread, and even the colour of the screw.
The Parts of a Screw
A screw is made up of four parts. The tip is the part of the screw that penetrates the material when driven in – and is either pointed or flat depending on the screw’s primary use and whether there is a pre-drilled hole. Self-tapping screws have a split point that cuts into the surface like a drill bit.
The screw thread wraps around the shank. These parts of the screw drive into the material and secure it. There are different types of shanks and threads, including twinthread screws which have two threads running along the shank and can be driven and removed faster, and hold materials more securely.
The head of the screw differs across screws and determines the drive type, meaning the type of screwdriver you’ll need to turn it. Each drive type has its own pros and cons, such as higher or lower torque – also known as the force required to rotate the screw.
Types of Screws
There are a wide range of screw types available, each one for a different purpose. Using the correct screw will mean the material is more secure and less likely to be damaged. You'll also find some screws are better suited for extreme conditions such as marine environments, which means they'll last far longer when exposed to the elements.
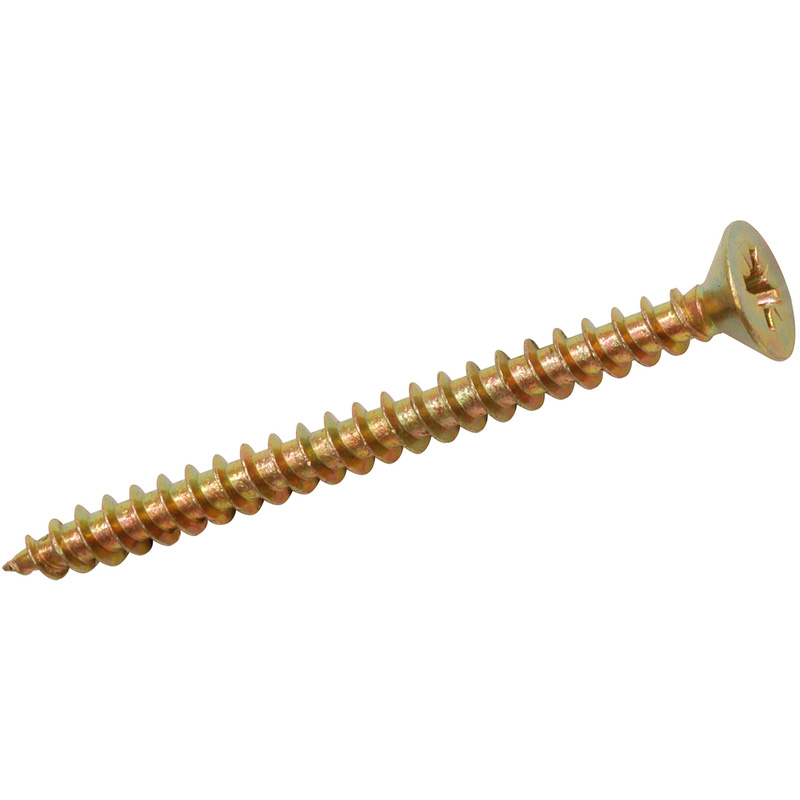
Wood Screws
Wood screws, as the name suggests, are made for use in hard and soft woods – as well as MDF and chipboard. They’re one of the most popular and inexpensive types of screw available. They’re stronger than nails because the threads bury themselves into the wood and create torque between the screw head and the wood.
They’re easier to install than other screws because of the very sharp tip, whether you’re driving into hardwood, softwood, or particle board.
If you’re drilling into hardwood, you may want to consider drilling a small pilot hole because most wood screws have a Phillips head which offers less torque – meaning you may struggle getting the screw into harder surfaces.
Advantages
-
Versatile and inexpensive
-
Easy to install because of a very sharp tip
-
Threads create torque between wood pieces and screw head
Things to Consider
-
For hardwood, a pre-drilled pilot hole can help installation
-
Most have Phillips screw heads, which offer less torque than other drill head types
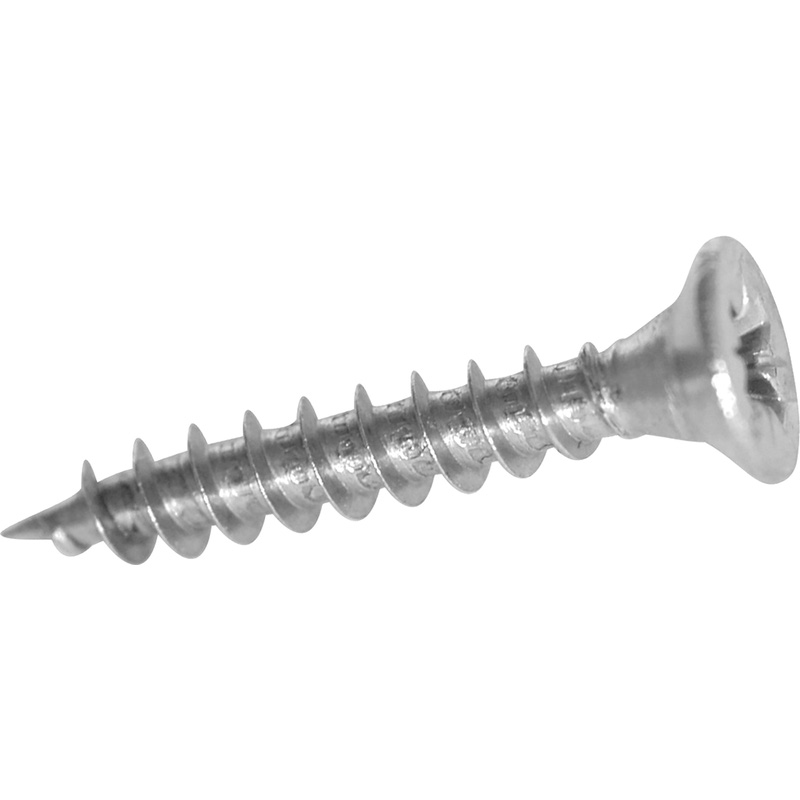
Stainless Steel Screws
Stainless steel screws are used for various situations such as building, construction, renovation and home improvement. They’re suitable for both hardwood and sheet metal, and ideal for outdoor use because they’re naturally rust proof and resistant to corrosion.
They can tolerate very high and low temperatures, and are suitable for boats and salty environments, making them very versatile.
Although stainless steel screws are versatile and strong, you should consider specialist screws for different purposes such as decking or roofing. These will be made especially for these environments, keeping the specifics of the surfaces and conditions in mind.
Advantages
-
High corrosion and rust resistance
-
Suitable for extreme environments
Things to Consider
-
Use specialist screws where possible
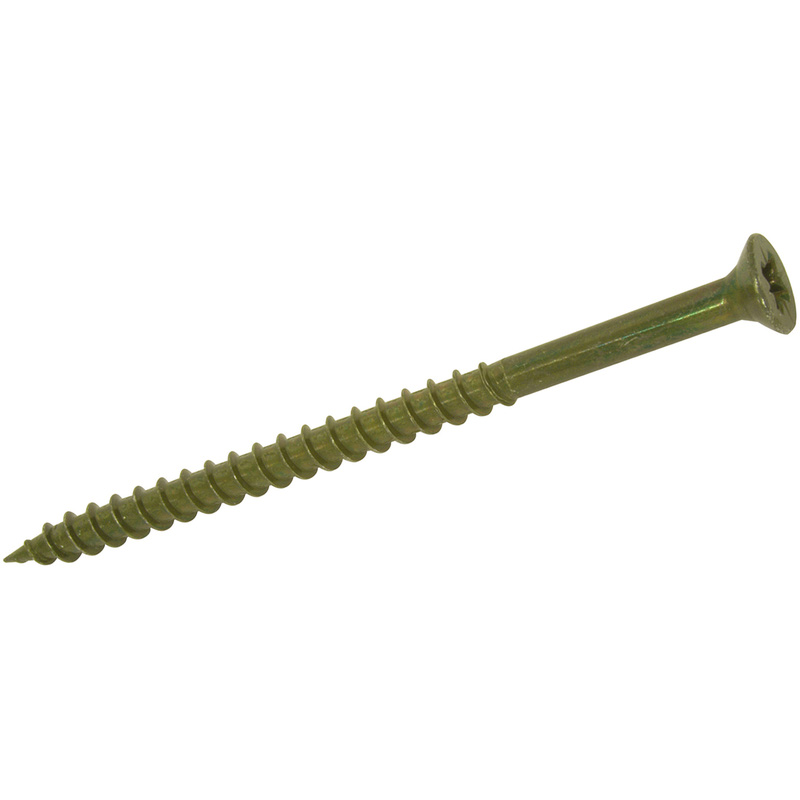
Decking Screws
Decking screws are used to attach pieces of outdoor decking to each other. They’re specially designed for outdoor use, and are made of hardened steel with a corrosion-resistant coating to protect from the elements and foot traffic.
The shank of decking screws is partially threaded and tapered to a sharp point, which locks the screw in place – meaning they’re highly secure. They also have a countersunk, torx head which allows greater torque to be applied for a tighter fit.
In marine environments, stainless steel screws will be a better option because they are slightly more corrosion resistant for the harsh, salty conditions.
Advantages
-
Corrosion-resistant coating protects from the elements
-
Breaking fins help lock the screw in place for greater security
-
Countersunk torx head allows greater torque to be applied
Things to Consider
-
Not as corrosion resistant as stainless steel
-
Less suitable for marine environments
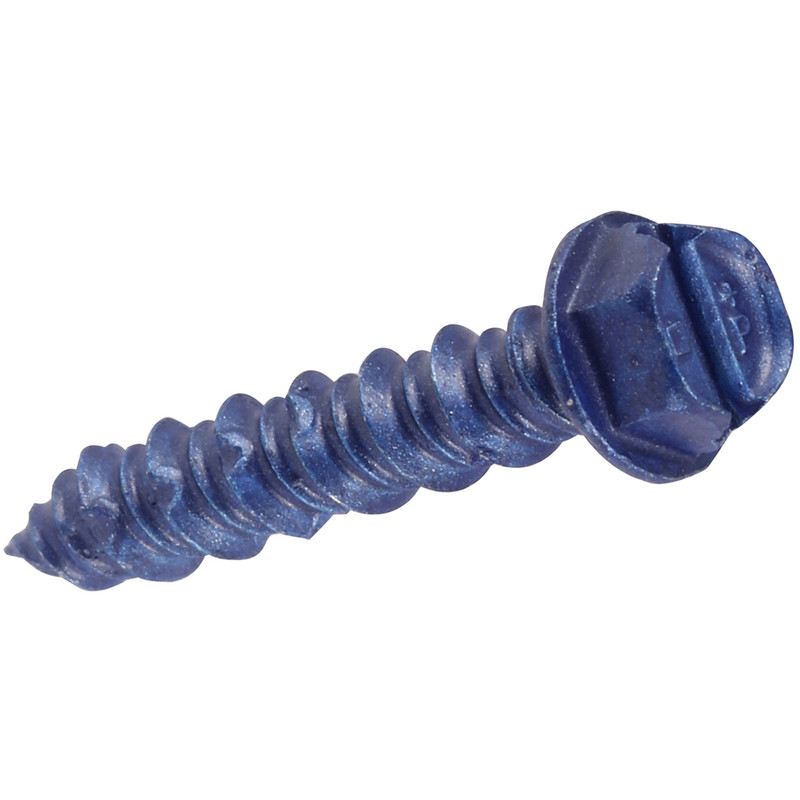
Speciality Screws
Each project will have different requirements, and you may find that speciality screws will be better suited to your situation. They come in a wide range of thread, head and shank types to suit each specific project, giving you peace of mind that you won’t need to replace fixings regularly and you can trust that they’ll stand up to their environment.
For example, confirmat screws are designed for furniture assembly, whilst a self-countersink screw is best for walls and floors for a flat, seamless finish. You’ll also find various corrosion-resistant screws for outdoor use, alongside many others.
Choosing a speciality screw over a generic type such as stainless steel or wood screw may come at a higher cost which you’ll need to consider. However, it’s always best to use the right fixing for specialist jobs as they’ll stand up to the task, last longer, and not cause damage to your surfaces.
Advantages
-
Less damage caused when using the appropriate screw
-
Able to deal with harsh pressures of the environment where necessary
-
Less likely to need replacing if you use the correct screw for the job
Things to Consider
-
Higher cost than more common screw types
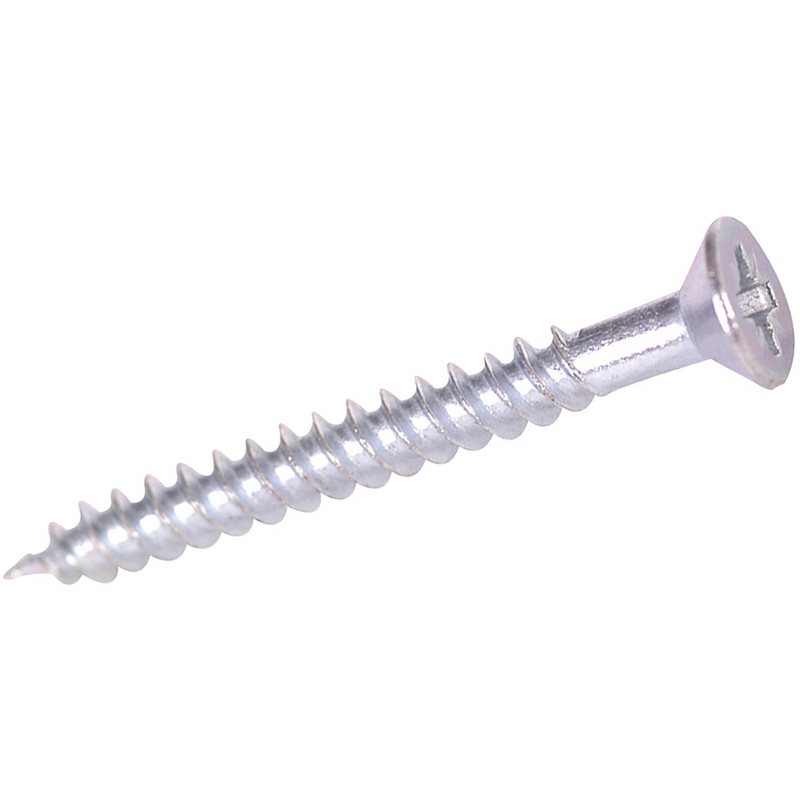
Twinthread Screws
Twinthread screws, also known as double thread screws, are used for hardwood, softwood, masonry with wall plugs, or for fixing plasterboard or fibreboard to timber studs. They have two threads running along the shank which means they can be installed and removed twice as fast as a single thread screw – perfect for jobs requiring a lot of driving into surfaces.
As well as being quicker and easier to install, they can provide a more robust fastening as they create more torque between the surfaces. They use a pozidriv drive type in order for more torque to be applied during installation – ensuring a more secure fixing.
Because of the extra benefits offered by twinthread screws, they generally come at a higher price than their single thread counterparts.
Advantages
-
Versatile across wood, masonry and plasterboard surfaces
-
Install and remove twice as fast as single-thread screws
-
Provide a robust fastening
Things to Consider
-
Often more expensive than single thread alternatives
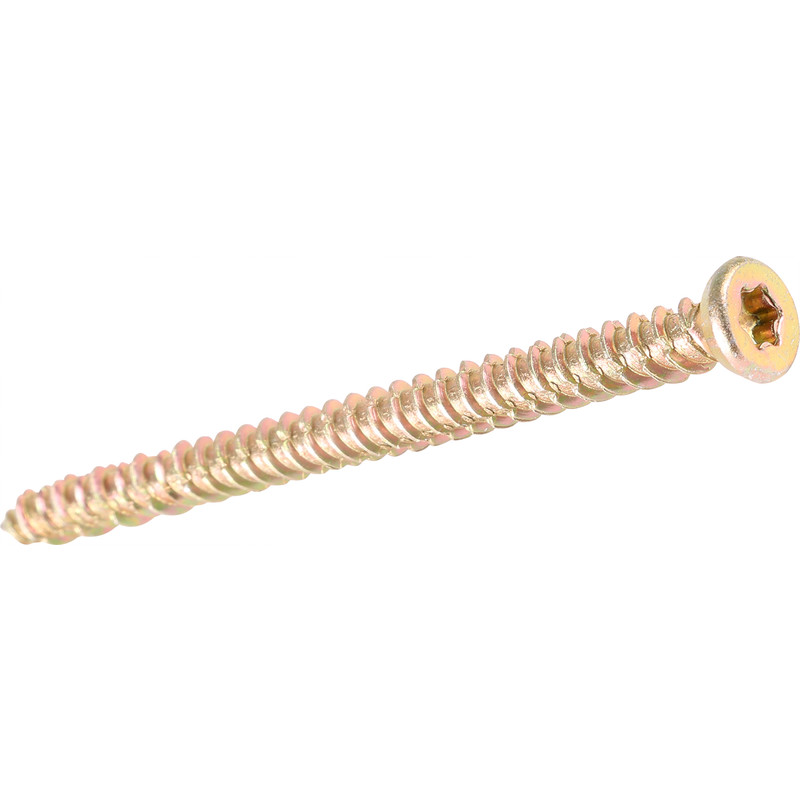
Masonry Screws
Masonry screws, also known as concrete screws, are used for a wide variety of materials including brick, concrete, block and mortar joints. They’re suitable for heavy-duty applications, making them a stronger, more robust alternative to other screws.
With a long body and deep, full thread, masonry screws offer superior security when installed. Typically made from carbon steel or stainless steel and zinc-plated for corrosion resistance, these screws are built to last. They’re designed for quick and efficient installation in the hardest surfaces.
Because of the strength of masonry, a pilot hole is highly recommended to make installation easier and to avoid damage to the surface or the screw. They can also be pricier than more common types of screw, but there’s no comparison when it comes to strength!
Advantages
-
Suitable for a wide range of heavy-duty masonry, including outside
-
Unique structure offers extra resistance and security to the fixing
-
Designed for quick and efficient installation in the hardest surfaces
Things to Consider
-
Higher cost than more common screw types
-
Pilot hole recommended to avoid damage to the surface or screw
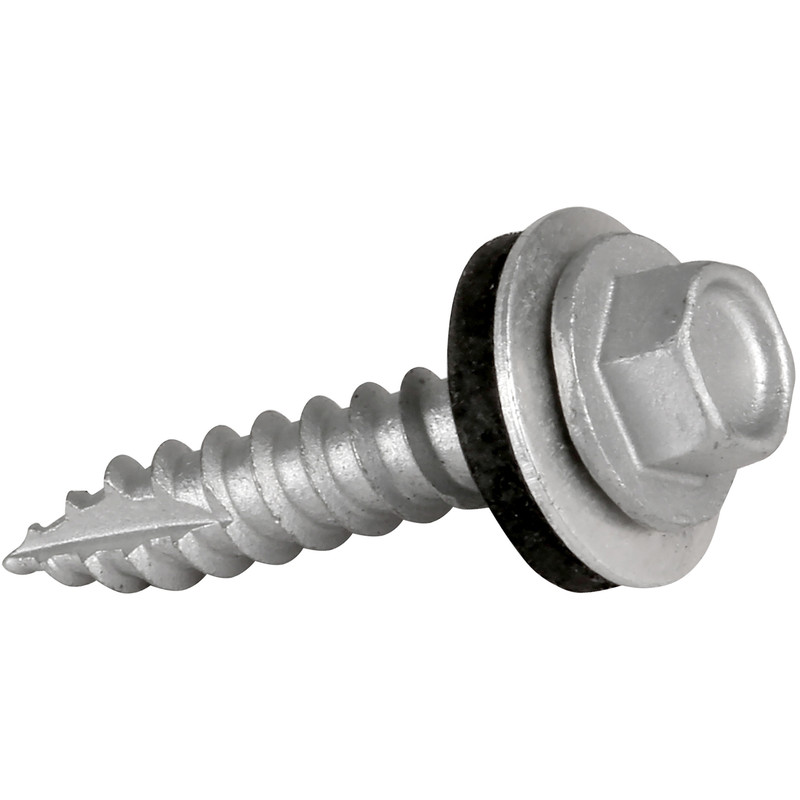
Self-Drilling Roofing Screws
Self-drill roofing screws don’t need a pilot hole, thanks to the tip of the screw resembling a drill bit – essentially, they drill their own hole into the surface on the way in. They’re ideal for materials such as wood and metal, and are mainly used in roofing projects but can be used elsewhere if necessary.
As no pre-drilling is required, they make less mess and allow for a speedier installation. Self-drilling roofing screws are also corrosion and rust resistant, perfect for outdoor environments and harsh weather. Some self-drill roofing screws even come with a bolt-like head and a washer for easy tightening and loosening.
When removing self-drilling screws, the threads can strip – meaning you’ll need a new, larger screw to secure the surface if necessary. Be wary of the amount of force and RPM you’re applying when driving in self-drilling screws, as the tip is susceptible to melting, chipping or splitting if too much force is applied.
Advantages
-
Mess-free installation
-
Speedy – no need to pre-drill holes
-
Corrosion and rust resistant
Things to Consider
-
Threads can strip during removal
-
Excessive force could damage the tip
-
Over or under tightening could create leak points
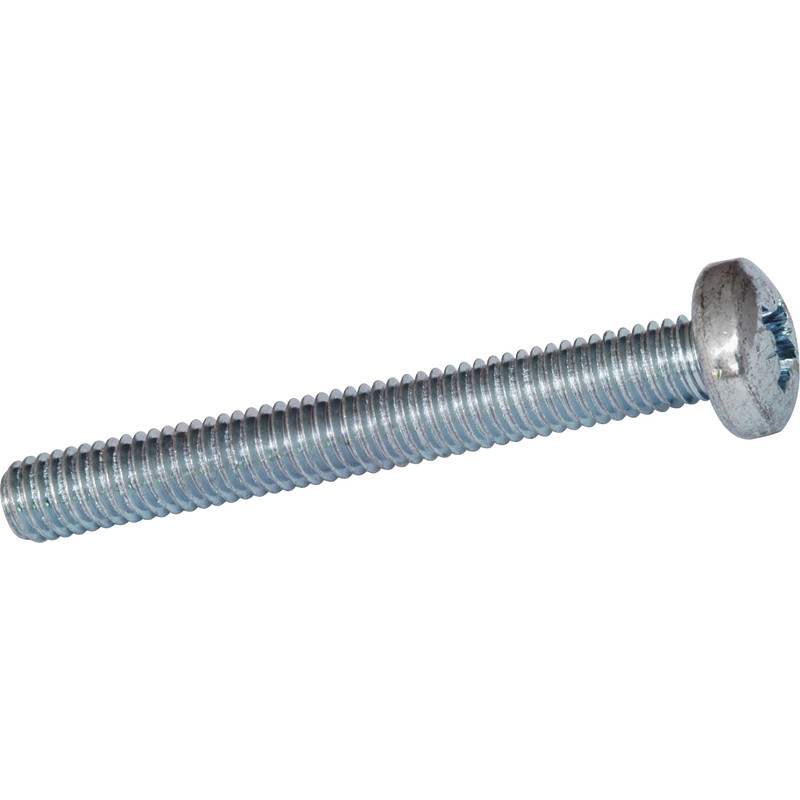
Machine Screws
Machine screws are a common type of fixing, often used on electronic devices, machinery and vehicles – whether you’re a tradesperson or DIYer, you’ll probably have come across them. They’re used in pre-drilled holes because they have a flat tip.
Machine screws are threaded along the entire shaft, making them very secure in the surface. They’re designed to be easily and quickly installed with a screwdriver, making them very DIY-friendly.
You’ll need to have a pilot hole drilled before driving the screw, which can be difficult in some surfaces. Some machine screws come with a nut for extra security, but you need to ensure the nut thread matches the screw or you’ll have trouble driving the screw in.
Advantages
-
Fully threaded, making them very secure
-
Wide variety of sizes for different projects
-
Easily installed using a screwdriver
Things to Consider
-
Pre-drilled hole is necessary because of flat screw tip
-
If using with a nut, the nut threads need to match to the screw threads
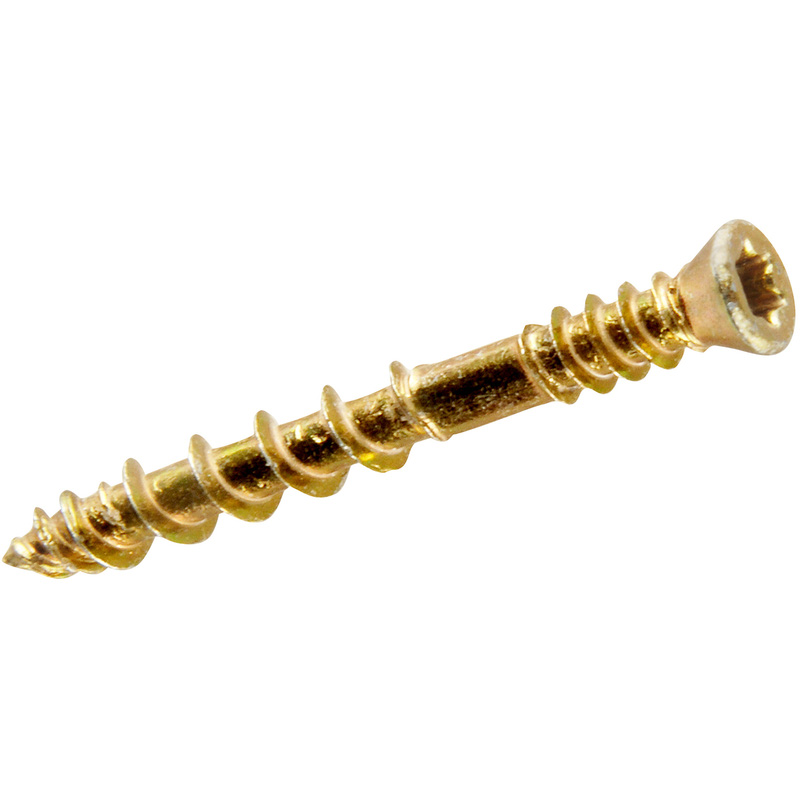
Flooring Screws
Flooring screws can be used on a wide range of flooring types, including softwood, hardwood and fibreboard. They’re easy to install, discreet in the floor, and hardwearing to cope with a lot of foot traffic. They often have a torx or pozidriv drive type, meaning a high level of torque can be applied for a secure fixing.
There's generally no pre-drilling required, and flooring screws are designed to prevent floorboards from splitting. The secure fit when using flooring screws compared to a generic screw results in quieter, non-squeaking floors.
You’ll want to consider a small, undercut head to prevent splitting, reduce rough edges on the screw head (burrs), and conceal the fitting.
Advantages
-
Easy to install, discreet, and hardwearing
-
High torque can be applied for a secure fit – reducing squeaky, noisy floorboards
-
No pre-drilling required
Things to Consider
-
Consider a small, undercut head to prevent splitting and conceal the fitting
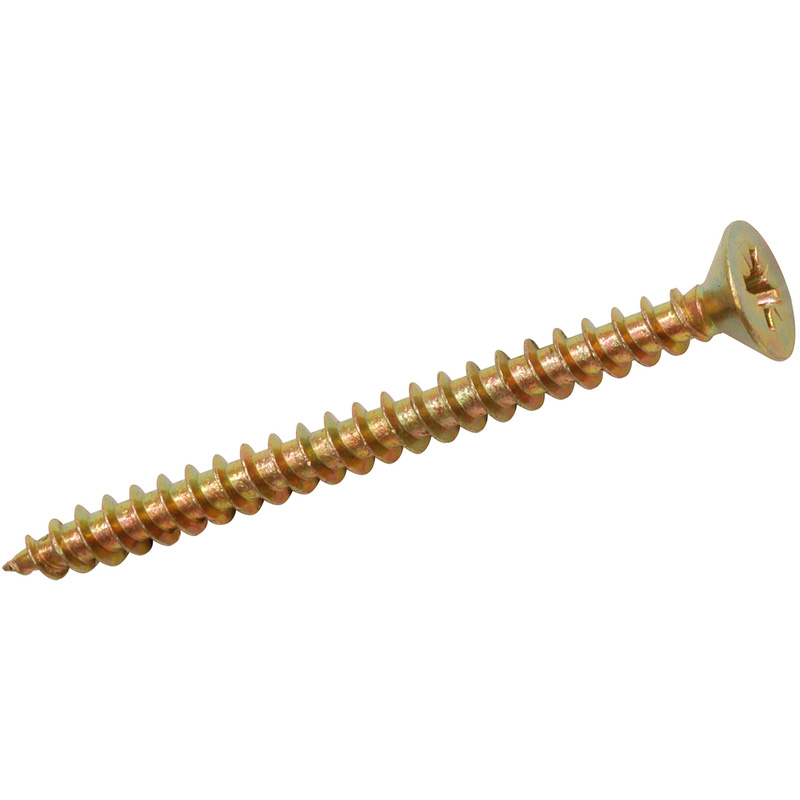
Self-Tapping Screws
Self-tapping screws create the thread as it’s being driven into the material. They’re not to be confused with self-drilling screws, which create their own pilot hole. Self-tapping screws ensure a strong, tightly fitting thread and are a very secure type of fixing.
They’re compatible with a range of soft materials that could be susceptible to damage, such as soft and hard wood, metal, and plastic. There are a range of types of self-tapping screw, including zinc plated which can offer corrosion resistance for outdoor use.
Unlike self-drilling screws, self-tapping screws require a pilot hole before installation to avoid cracking or damaging the material you’re working with. This takes extra time, particularly if you’re needing to install a large number of screws. Self-tapping screws are also not suited to heavy-duty jobs, meaning their use is limited.
Advantages
-
Strong, tightly fitted type of fixing
-
Compatible with a range of materials typically susceptible to damage
-
Zinc-plated options can offer corrosion resistance
Things to Consider
-
Require a pilot hole before installation
-
Not suitable for heavy-duty jobs
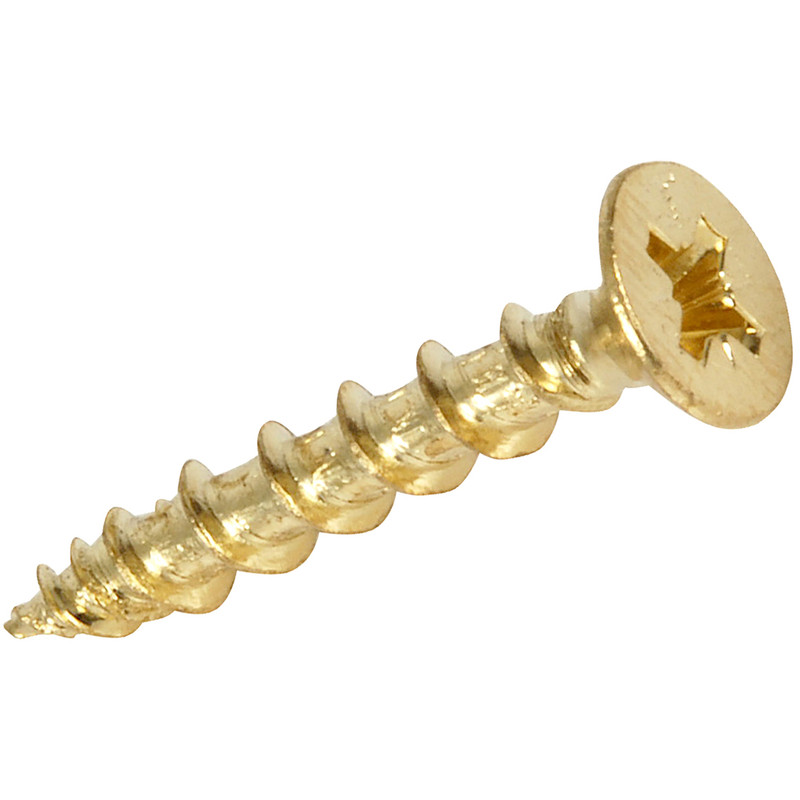
Brass Screws
Brass screws are generally used for putting furniture together and installing doors. Their natural rust resistance makes them more versatile and longer lasting than a generic steel screw – making them suitable for outdoor use.
Brass is also an aesthetically pleasing material for screws, as their natural colouring works well with wooden surfaces.
Brass screws often come at a higher cost than generic screws because of their natural rust resistance. For the eco-conscious, the material can be harder to recycle and may require extra effort to find a way to dispose of them correctly. Additionally, brass is a soft metal and should be avoided for use with heavy-duty materials.
Advantages
-
Naturally rust resistant and anti-corrosive
-
Versatile and long-lasting
-
Aesthetically pleasing
Things to Consider
-
Higher price tag compared to generic screws
-
More difficult to recycle
-
Soft metal – not recommended for heavy-duty materials
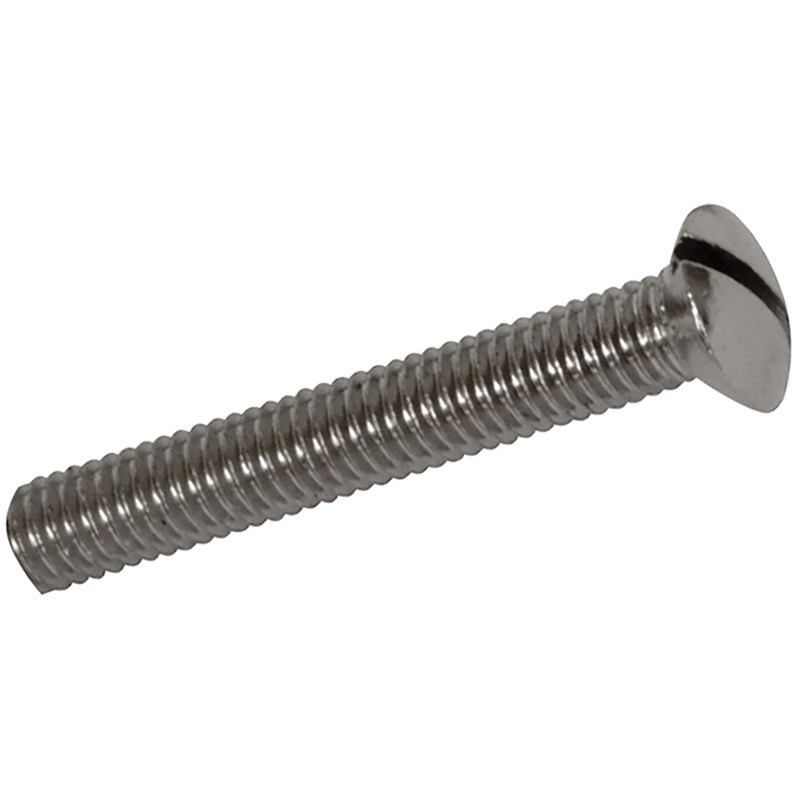
Electrical Screws
Electrical and switch box screws are designed to offer a secure fix when installing and repairing sockets in residential and commercial buildings. Their most common use is attaching faceplates to their back boxes. The screw provides a strong fix because electrical screws are fully threaded. In any situation, this is important – but arguably more so when dealing with electrics.
They’re often brass or zinc-plated, making them long lasting, and resistant to corrosion and rusting. Electrical screws generally have a slotted drive type, so the correct amount of torque can be applied without damaging the surface or the screw.
In most cases, pre-drilling will be required as they generally have a flat tip – similar to machine screws. This will add to the time required, particularly if you have a lot of screws to install.
Advantages
-
Fully threaded screw, providing a strong fix
-
Generally made from corrosion and rust-resistant materials
-
Slotted drive type ensures the correct amount of torque is applied
Things to Consider
-
Pre-drilling required because of the flat tip
Screw Drive Types
The drive type of a screw refers to the tool you need to install it. Every screw is designed with a different shaped recess in the head which aligns to a different tool – for example, a Phillips drive type needs a Phillips screwdriver.
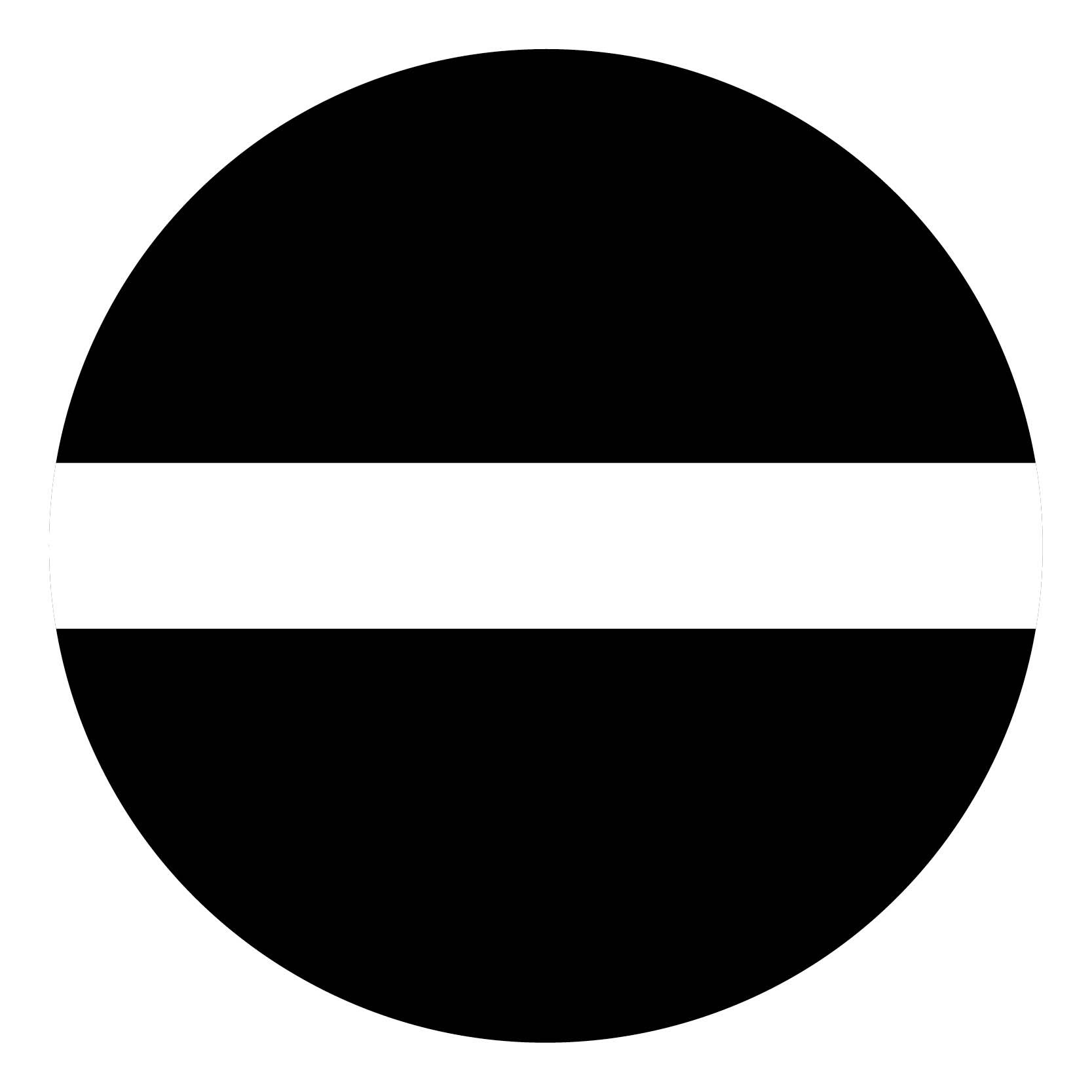
Slotted Screws
Slotted screw heads have a horizontal slot in the head and are driven by a flathead screwdriver. They’re suitable in cases where minimal torque is required, such as in carpentry or attaching faceplates on electrics.
They’re not suitable for use with power tools because the drill bit would slip out of the slot – causing damage to the screw and the material.
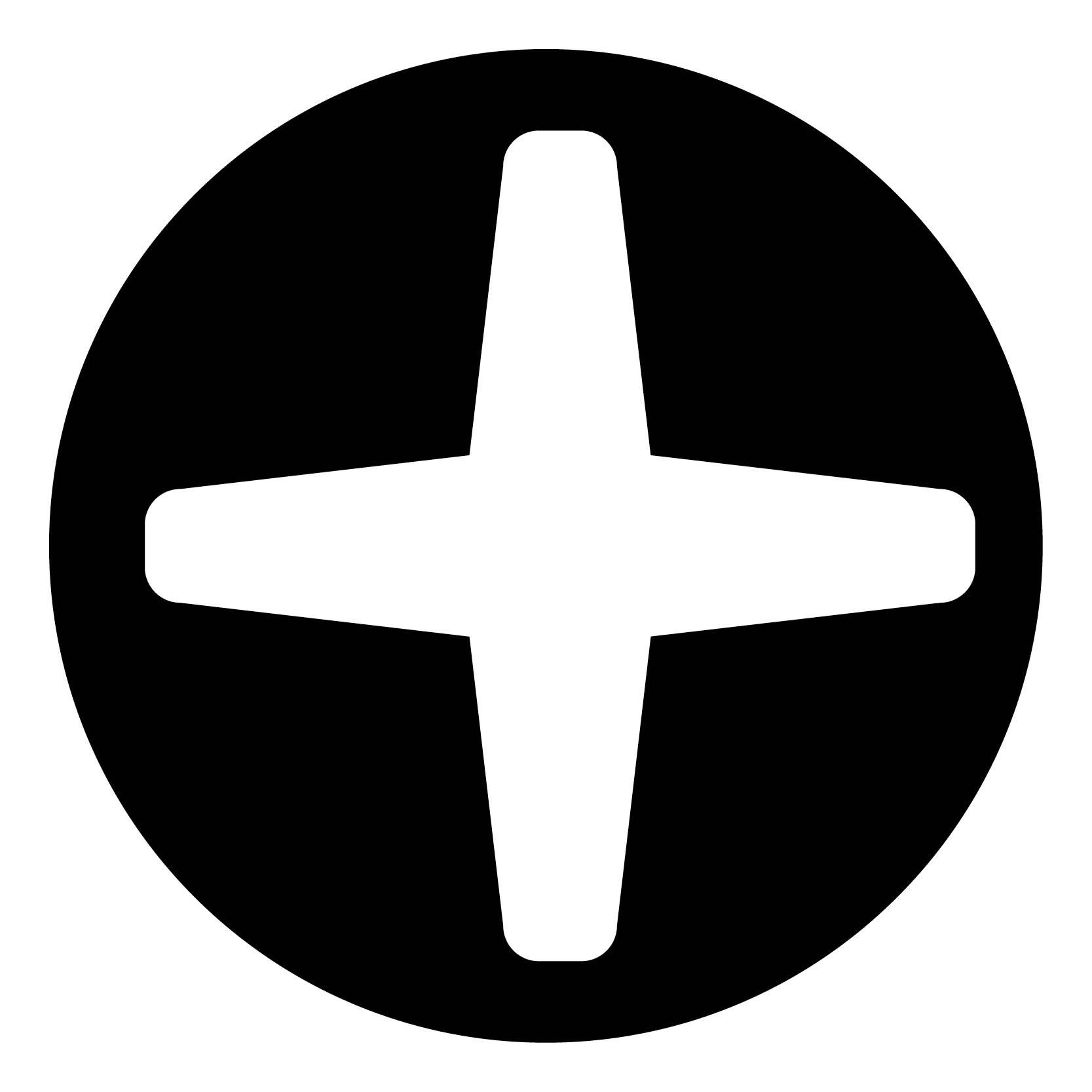
Phillips Screws
Phillips drive types are very common and well-known, recognised by a cross on the top of the screw head. When it comes to power tools, screws with Phillips heads are a better option than slotted heads. This is because they have a lower 'cam out' potential – when the driver slips out of the slot. Phillips heads also offer greater precision with alignment and are less likely to cause damage to the driver, fastener, and surfaces compared to slotted heads.
If torque gets too high, Phillips drive types have the tendency to ‘cam out’. However, some people find this helps as it means you can avoid over tightening the fasteners and damaging the material.
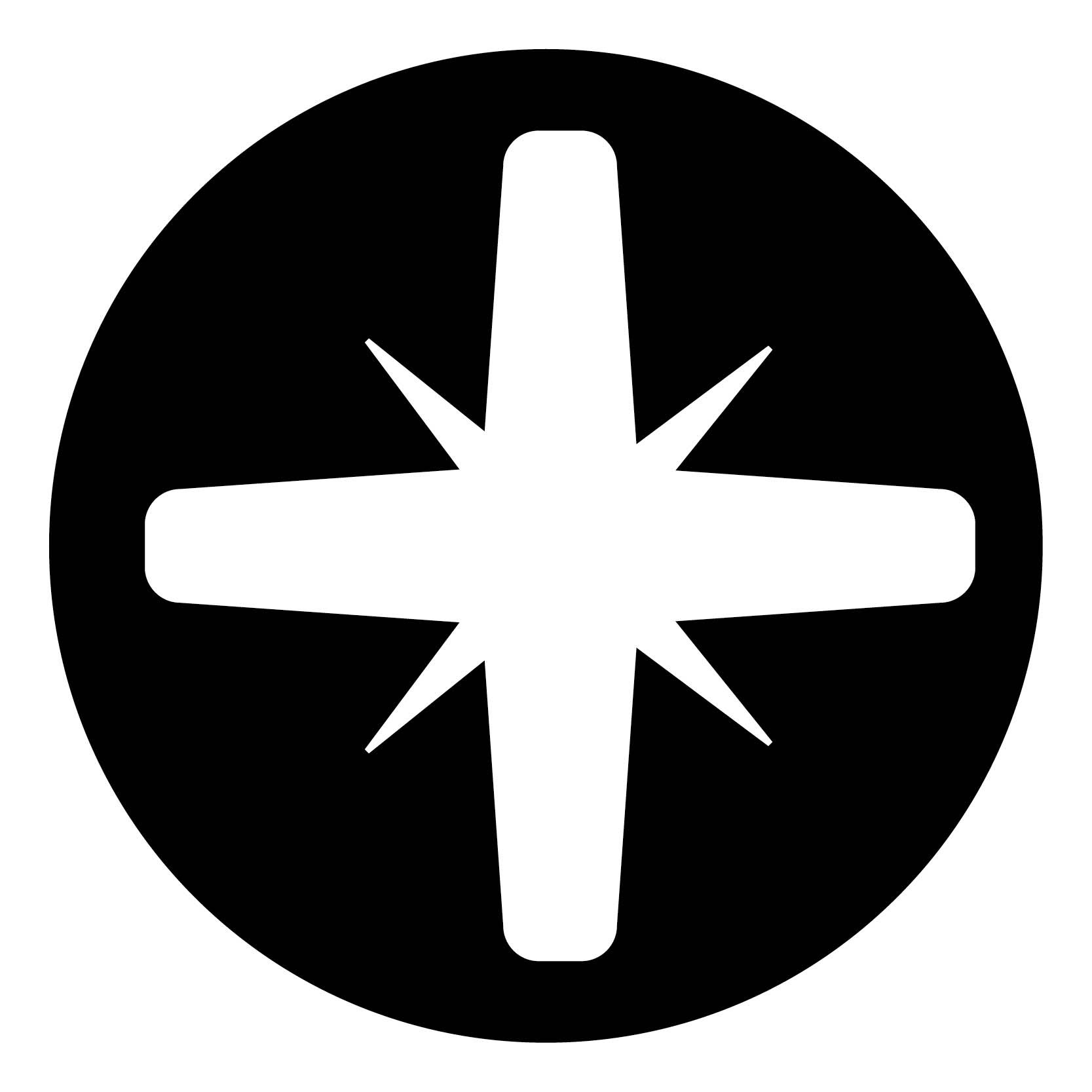
Pozidriv Screws
Pozidriv heads are thought of as an improvement on the Phillips drive type. They have four extra notches diagonally on the screw head which allows for greater support for the driver, and torque can be increased with a lower chance of ‘cam out’.
The main disadvantage of a Pozidriv screw is that a Phillips driver can be mistakenly used because of their similar design – these drivers often round off the corners of the head, even at a lower torque, and can lead to a stripped screw.
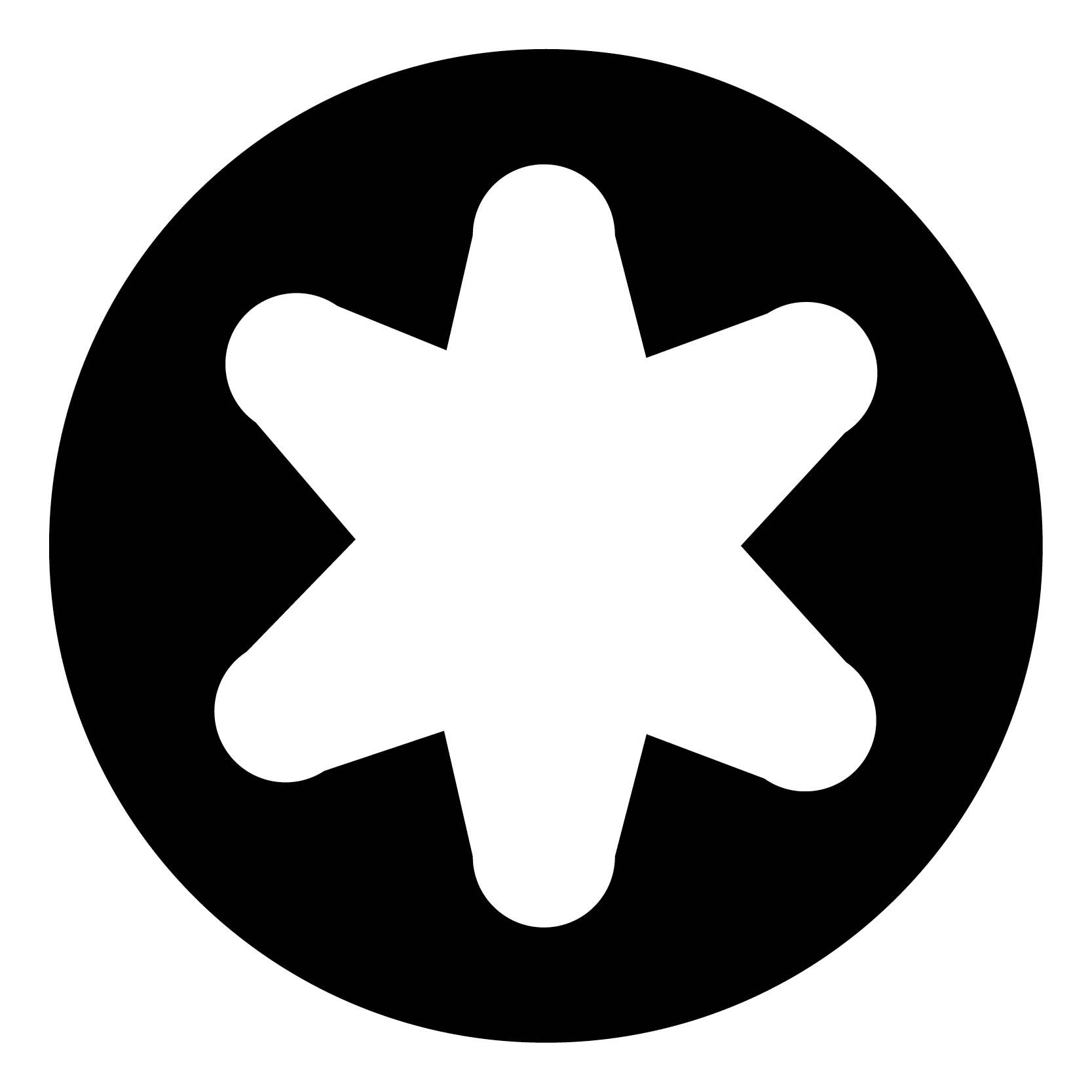
Torx Screws
Torx drive types are recognised by their 6 point star-shaped head. They’re commonly found on vehicles, hard disk drives, computer systems, and electronics. Torx heads can transmit a high amount of torque compared to Phillips and Slotted drive types.
Torx heads are generally less available than other, more generic drive types such as Phillips. This means you may find that Torx heads are more expensive, because you’ll be limited to branded screws instead of unbranded.
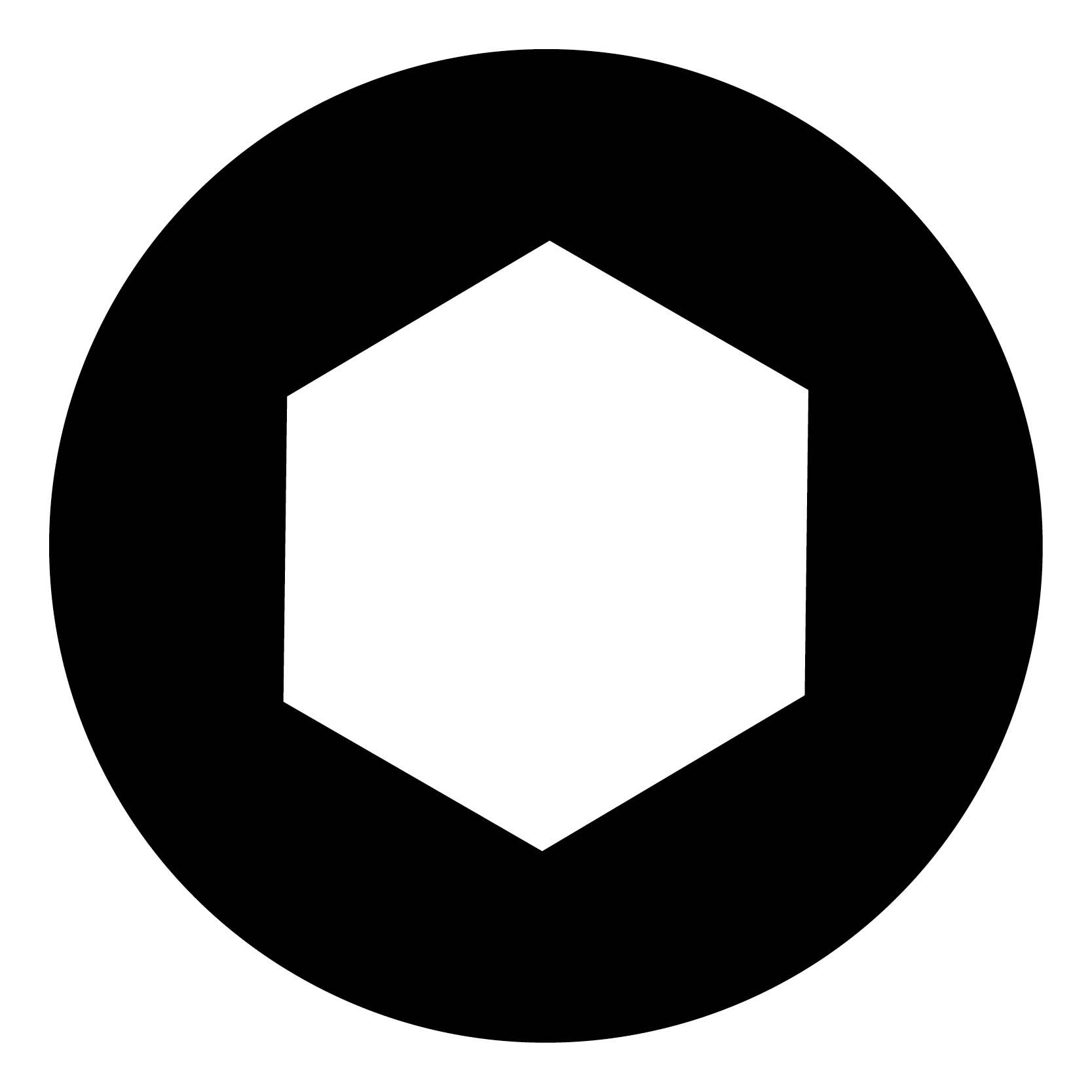
Hex Screws
Hex drive types, also known as Allen screws, are recognised by their 6-sided, hexagon-shaped heads – and are operated with a hex key or allen key. In small spaces or where there are obstacles, smaller turns can rotate the screw compared to other types, and they offer a high level of torque for a secure fit.
With any screw, it’s important to use the right size driver. However, if you use the wrong size driver with a Hex screw, you could strip the screw head and make it circular – meaning you won’t be able to use it anymore and it’ll be hard to remove.
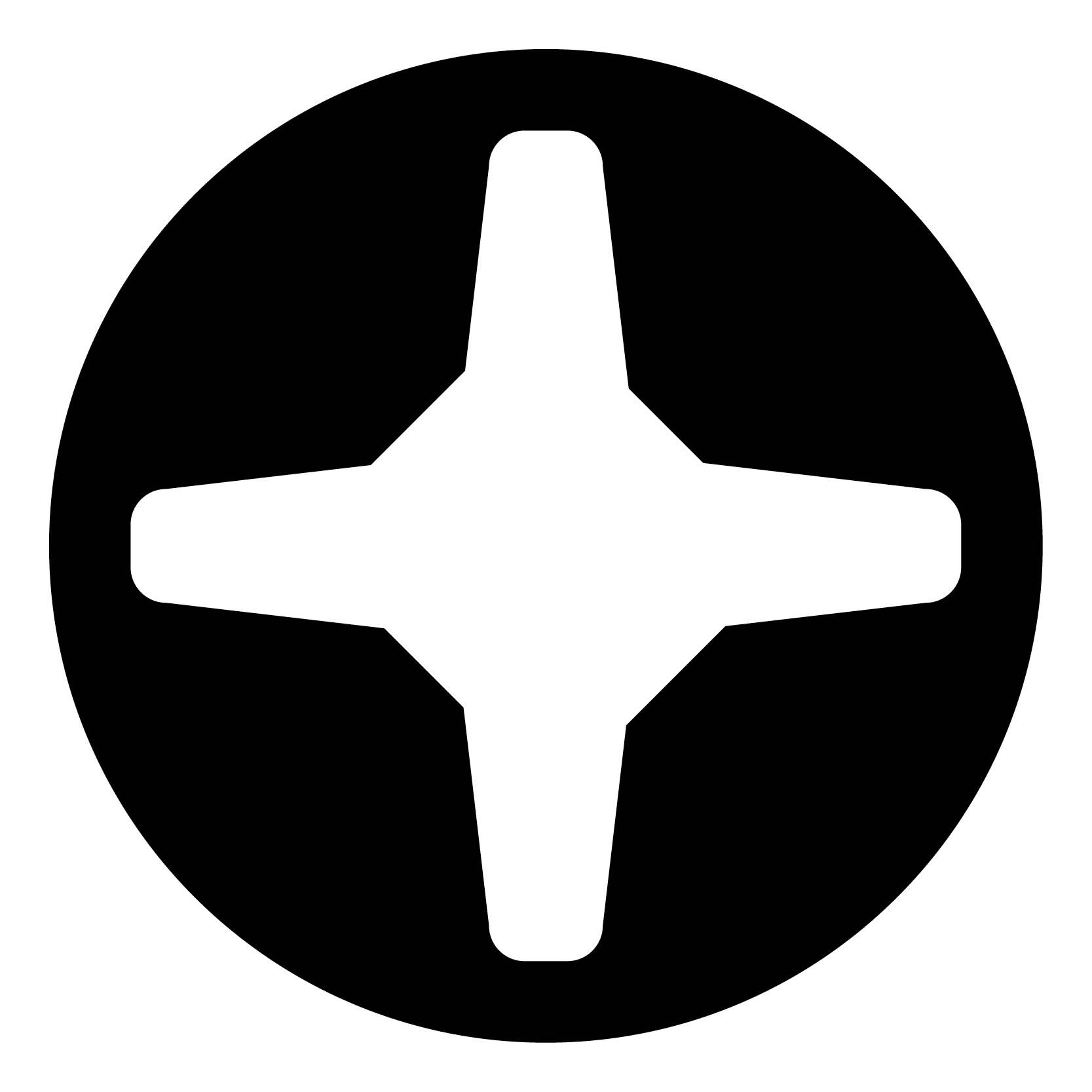
PoziSquare Screws
In the same way a Pozidriv is an improvement on the Phillips, a PoziSquare is an improvement on the Square screw, commonly used in vehicles. There are ribs on the driver that go into recesses in the screw head – this reduces stripping, improves off-angle durability, and fits in cleanly to make driving easier.
PoziSquare heads are less common than other types of screws, meaning you’ll be more likely to find branded, pricier options rather than unbranded. If you’ll be using a lot of PoziSquare screws, it could bump up the price of your project compared to using Phillips heads.
Screw Head Types
The head type of a screw generally refers to how it looks against the surface when it’s installed. Sometimes there are technical reasons for a certain head type – such as bugle heads being better for soft materials like drywall – and other times it is more decorative, like a countersunk head to camouflage the fixing.
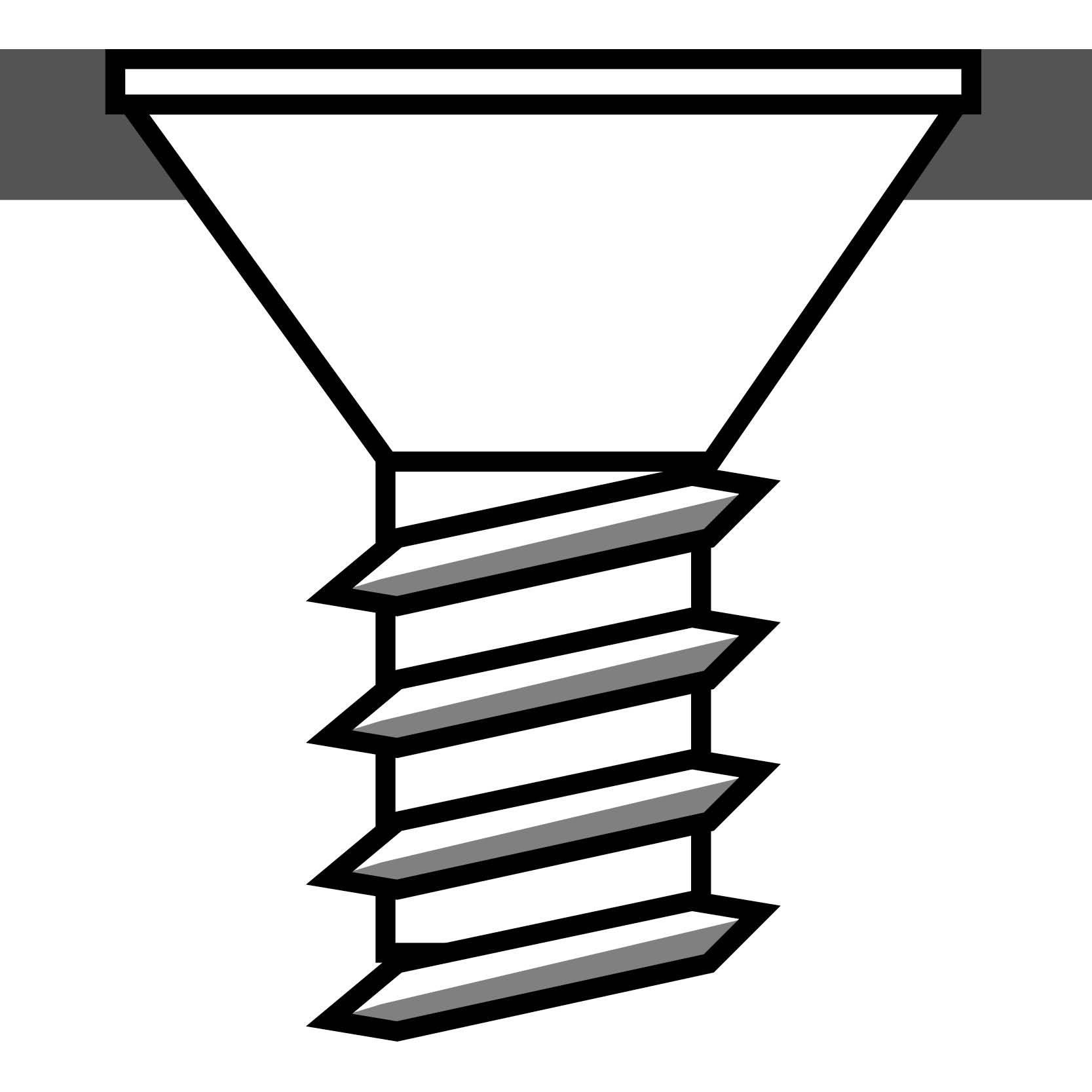
Countersunk Heads
The most common type of screw head type is a countersunk head. This is a type of flat head screw which tapers down into the shank. Counterhead screws are popular because the head remains flush with the surface, making it easier to camouflage.
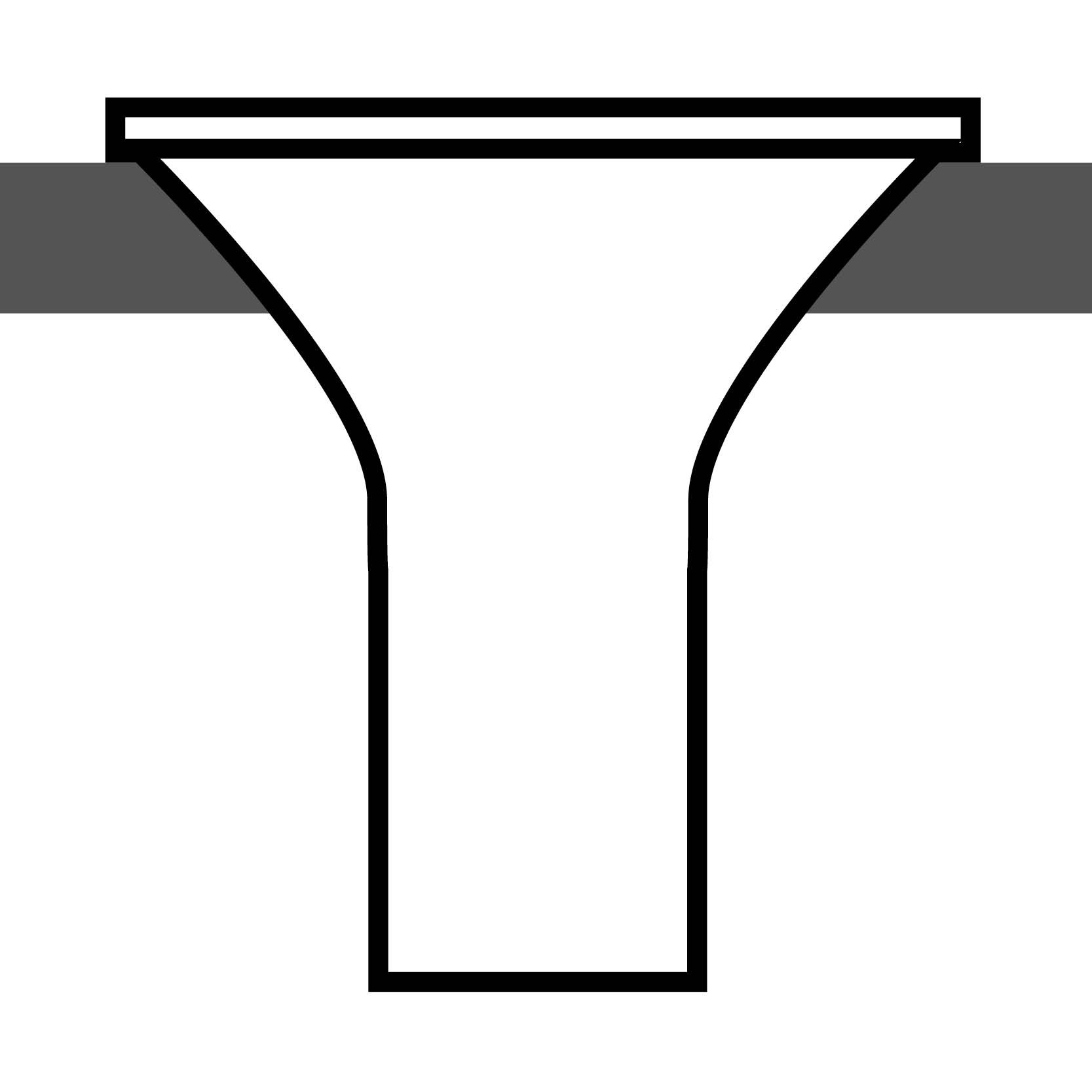
Bugle Heads
Bugle head screws are very similar to countersunk screws, but better for softer materials such as drywall because the sides are rounded when the head tapers into the shank. This puts less pressure on the softer material, so is less likely to cause damage.
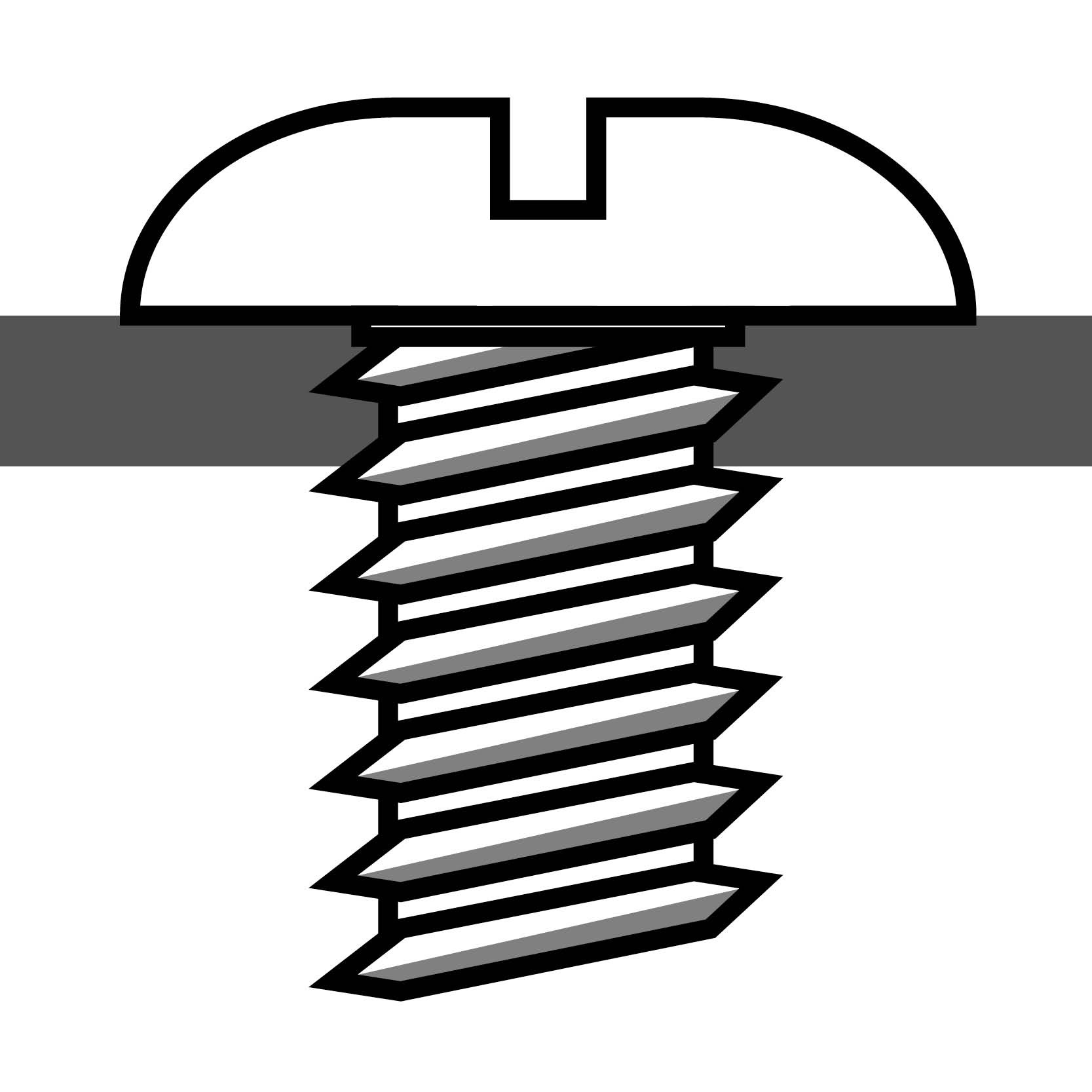
Pan Heads
Alternatively, you can choose a pan head screw which is slightly domed on the surface of the material – taking their name from an upside-down frying pan. This type of head is very useful when a high level of torque is required, as there is extra space to provide a deep socket for a driver.
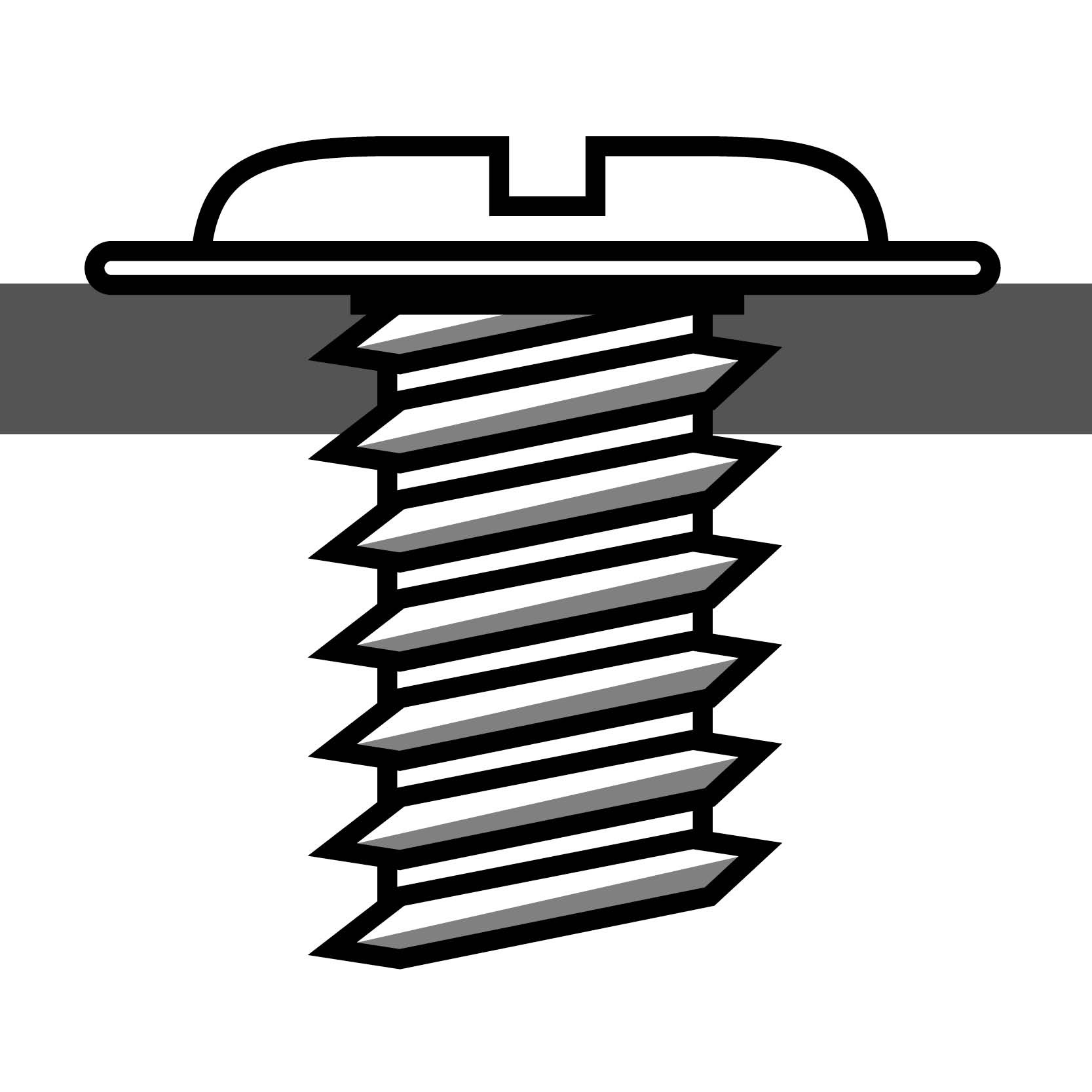
Button Heads
A button, or round head screw, sits above the surface when fastened and is often used when a decorative finish is required – such as securing a mirror. You may also find button head screws in mechanical or automotive projects because they’re well suited to Hex drive types – the rounded head providing a deep socket for high levels of torque.
Key Screw Features
Thread Type
A screw can either be fully or partially threaded. A fully threaded screw has threads running from the tip to the head – meaning every part of the screw is secured in the material.
A partially threaded screw, as the name suggests, only has threading on part of the screw. This type of screw has its benefits – such as when the materials will be put under more stress and could get damaged.
Length
The screw you’re using needs to be the right size for the surface and the project, or you could damage the surface, the driver, or the fixing itself.
Screws that are too long could pass all the way through the material, whilst screws that are too short are unlikely to be strong enough to hold the materials together.
Diameter
The diameter of the screws is also important, as thicker screws may split more delicate materials such as wood – where narrower screws should be used instead. However, thinner screws could be bent out of shape if used in heavy-duty projects.
On twinthread screws, you may see diameter referred to as gauge.
Colour
One of the main disadvantages of screws is that they’re visible on the surface of the material. For this reason, you may want to find a colour screw that matches the surface to blend in.
At Toolstation, you’ll find a range of colour screws including black, tan, green, yellow, silver, blue, red, and white.
Finish and Material
The finish and material of a screw determines both the colour, and the properties it has. For example, the best type of screw for outdoor use is stainless steel because it is resistant to rust and corrosion.
There are other screws resistant to rust and corrosion, such as zinc and chrome-plated screws, black phosphate, and brass screws. However brass screws, for example, are softer so less suited to a lot of outdoor heavy-duty projects.